For even more competence in battery production in the Ostalb region of GermanyHS Aalen receives around 400,000 euros in funding for joint battery research project with automation specialist VAF
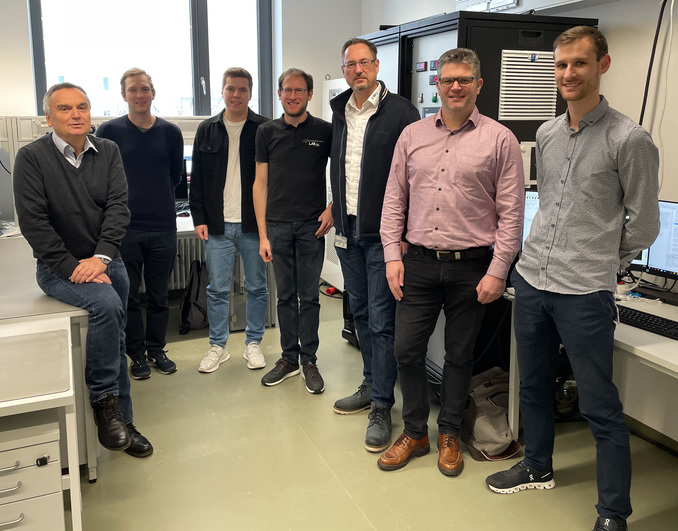
Zum Auftakt des neuen Batterie-Forschungs-Projekts trafen sich die Partner an der Hochschule Aalen. Auf dem Bild von links: Prof. Dr. Heinrich Steinhart, David Kolb, Stephan Koch, Markus Hofele (alle Hochschule Aalen), Thomas Braun, Tobias Huber und Thomas Stippler (alle VAF). Foto: © Hochschule Aalen | Andrea Heidel
Innovative energy storage concepts are more in demand than ever, they make an important contribution to electromobility and are seen as a beacon of hope for the energy transition. However, the manufacturing processes of batteries involve complex steps in which there is still a lot of potential for research and improvement. In a freshly launched project, two research groups at Aalen University together with VAF, the automation specialist based in Bopfingen, now want to develop a novel, contamination-free dosing station for lithium-ion batteries. The state of Baden-Württemberg is funding the project with around 400,000 euros.
Lithium-ion cells are the key to mobile power supply and make electromobility not only possible but also practical. A wide range of mobile applications - from power tools and motor vehicles to large construction machinery - will be supplied with energy in the future thanks to efficient battery technology. This requires new storage technologies and efficient production processes, because the manufacture of lithium cells involves numerous, highly complex production steps.
In order to research these and further advance cell production expertise in the Ostalbkreis region, two groups of researchers at Aalen University have now received funding of around 400,000 euros. The "ELDosBATT" research project is being funded by the Baden-Württemberg Ministry of Economics, Labor and Tourism as part of the "Invest BW" program.
In addition to the LaserApplicationCenter (LAZ) at Aalen University around the President and LAZ director, Prof. Dr. Harald Riegel, the working group headed by Prof. Dr. Heinrich Steinhart from the Laboratory for Power Electronics and Electric Drive Technology (LEA) is involved in the project. The consortium also includes VAF from Bopfingen, a company that specializes in the development and construction of complex automation solutions for new technologies such as the production of battery cells.
"In the production chain of round cells and prismatic battery cells, we are developing new solutions in electrolyte filling and the subsequent laser welding process on arresters and battery housings as part of the research project," explains Markus Hofele, a doctoral student at the LaserApplicationCenter (LAZ) at Aalen University, who was in charge of applying for the project. "At its core, the goal is to develop a novel, contamination-free electrolyte dosing station for variable battery cell types," adds Prof. Steinhart.
Batteries are filled like canned fish
Inside, a battery consists of several rolled-up layers that are filled with an electrolyte liquid after being placed in a housing. The process can be imagined as in a fish can, Hofele describes: If the sardines are stacked nicely on top of each other in the can, a dosing station comes and fills up a precisely dosed amount of oil via a funnel. However, this is where the difficulties begin during cell filling: "The electrolyte seeps through only slowly to the bottom, so it must first be overdosed. But in no case so much that it overflows. Every milliliter really matters here." Even small deviations lead to capacity deviations or defects in the lithium cell. In addition, he said, contamination of the lid and contacts with electrolyte leads to defects in the welding process.
The project will last a total of two years and includes several subprojects: The working group around Prof. Steinhart is developing a novel, high-precision dosing station for electrolyte filling, and the LAZ is subsequently investigating the influence of different laser wavelengths in the case of different contamination states by the electrolyte solution. The LAZ team is also developing new welding strategies to better join the battery components. "We want to develop a robust process and, together with VAF, a prototype system for efficient cell production with low reject rates," Hofele summarizes. After all, the partner VAF not only develops systems for cell production, but is also closely networked with automotive manufacturers: "This is a real Ostalbkreis project with which we will further advance the competence for cell production in the Ostalbkreis."